Ansätze für einen geschlossenen Batteriekreislauf
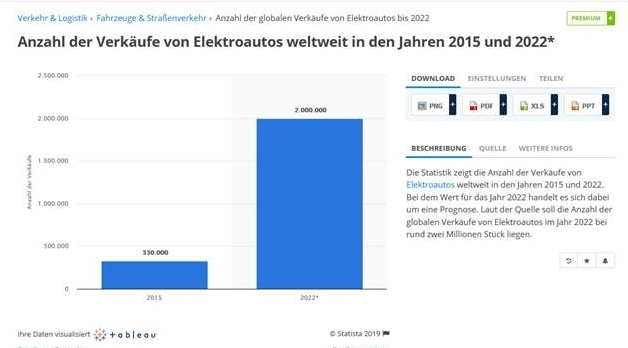
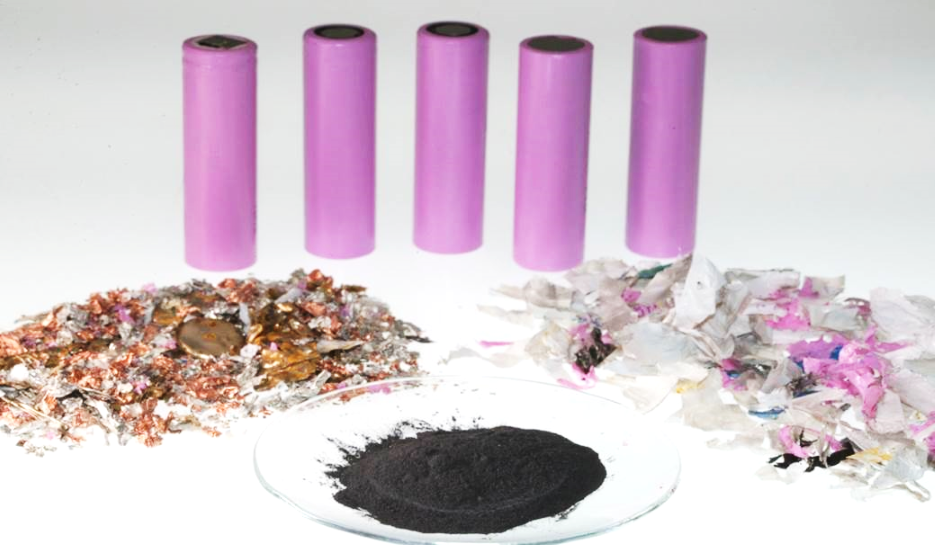
Die Elektromobilität ist eine strategische Säule für die Mobilitätswende hin zu nachhaltigeren und umweltfreundlicheren Antriebstechnologien. Eine Schlüsseltechnologie für den Erfolg der Elektromobilität sind Batterien bzw. Akkus für Fahrzeuge. Doch mit der steigenden Anzahl an elektrisch angetriebenen Fahrzeugen steigt auch der Bedarf für ein effizientes und umweltgerechtes Recycling ausgedienter Fahrzeuge und deren Komponenten.
In diesem Papier fassen die Forscher der Fraunhofer-Projektgruppe für Wertstoffkreisläufe und Ressourcenstrategie IWKS die wichtigsten Fakten zusammen, zeigen Herausforderungen und Lösungsansätze auf.
Der Markt der Elektromobilität wächst
Die Zahl der Elektroautos in Deutschland hat sich seit 2011 von 2.307 Elektrofahrzeugen auf 53.861 im Jahr 2018 gesteigert – bis 2022 sollen nach Plänen der Bundesregierung eine Million Elektroautos auf deutschen Straßen unterwegs sein (1). Im gleichen Maß wächst daher auch der Bedarf an Hochleistungsbatterien wie Lithium-Ionen-Akkus. Um diesen Bedarf zu decken, ist ein effizientes Recycling der Altbatterien unerlässlich. Im Jahr 2020 könnten laut Prognosen allein in den USA bis zu 500 Millionen Lithium-Ionen-Batteriezellen zur Entsorgung anfallen (2). Je nach technologischer Entwicklung könnte sich diese Zahl bis 2030 auf bis zu 4,5 Milliarden Batteriezellen steigern – ein rasant wachsender Abfallstrom. Dies betrifft nicht nur beispielsweise durch einen Unfall beschädigte Batterien, sondern auch intakte gebrauchte Batterien. Bei weniger als 80% ihrer ursprünglichen Ladekapazität ist für Traktionsbatterien normalerweise das Ende ihrer Lebensdauer erreicht, da dann die Reichweite des Fahrzeugs rapide abnimmt (3). Auch wenn Batterien nach ihrer Erstnutzung in Second und Third Life-Anwendungen genutzt werden, ist früher oder später eine Entsorgung notwendig. Hier gilt es, möglichst alle verwendeten Stoffe im Sinne einer geschlossenen Kreislaufwirtschaft zurückzugewinnen und wiederzuverwerten. Dies ist auch im Batteriegesetz (BattGDV) so festgelegt, wonach seit 2011 eine stoffliche Verwertungsquote von 50 Prozent der durchschnittlichen Masse sonstiger Altbatterien (unter die Li-Ionen-Batterien fallen) verpflichtend ist (4). Die Sammlung der Batterien kann entweder über die verschiedenen Rücknahmesysteme erfolgen oder direkt über ein herstellereigenes System. Die zu erfüllende Sammelquote liegt derzeit bei etwa 45 Prozent und errechnet sich aus dem Gewicht der Altbatterien, die im aktuellen Kalenderjahr gesammelt wurden im Verhältnis zu dem Gewicht der Batterien, die die Hersteller im aktuellen sowie in den beiden vorausgegangenen Kalenderjahren verkauft haben (5).
Ohne Rohstoffe keine Mobilitätswende
Um hohe Energien beispielsweise beim Einsatz in Elektroautos bereitzustellen, werden inHochleistungsbatterien spezielle Elektrodenmaterialien eingesetzt, die verschiedene kritische Rohstoffe wie Lithium, Kobalt, Nickel und Graphit enthalten. Die Nachfrage ist in den letzten Jahren enorm gestiegen: Über 40% des weltweit produzierten Kobalts wird für die Herstellung von Lithium-Ionen-Batterien verwendet (6). Kobalt wird aufgrund der geringen Reserven nur in wenigen Ländern der Welt abgebaut, darunter DR Kongo, Russland, Australien und Kuba. Die gesteigerte Nachfrage mit gleichzeitiger Abhängigkeit von Importen aus den Abbauländern hat zu einem massiven Preisanstieg geführt. Seit Mitte 2016 hat sich der Preis für eine Tonne Kobalt von 23.000 USD auf etwa 90.000 USD innerhalb von nur zwei Jahren fast vervierfacht. Die Industrie reagiert unter anderem damit, den Kobaltanteil so weit wie möglich zu reduzieren, um Kosten zu sparen.
Effizientes Recycling trägt zur Steigerung der Nachhaltigkeit der Elektromobilität bei
Das Ziel der Forschungsarbeit der Fraunhofer-Projektgruppe IWKS und anderer Forschungseinrichtungen ist es, zu einer nachhaltigen Entwicklung im Sinne einer ökologisch intakten, ökonomisch erfolgreichen und sozial ausgewogenen Welt beizutragen. Das Recycling von Traktionsbatterien aus Elektrofahrzeugen wird in den nächsten Jahren massiv an Bedeutung gewinnen. Die derzeitigen Kapazitäten werden in absehbarer Zeit von der Menge an Rückläufern überholt. Generell sehen die Forscher der Fraunhofer-Projektgruppe IWKS am Markt ein hohes Potenzial für die Weiterentwicklung des Recyclings von Altbatterien von Elektroautos – im Idealfall bis hin zur vollständigen Kreislaufführung. Das Recycling von Batterien ist allerdings nicht neu und wird bereits im Industriemaßstab umgesetzt. Dazu gibt es verschiedene Verfahrensansätze:
- Mechanisches Recycling: Schreddern und Mahlen, Abtrennung von Fraktionen, Rückgewinnung von Konzentraten
- Pyrometallurgisches Recycling: Aufschmelzen der Batterien zur Rückgewinnung von Kobalt, Nickel und Kupfer
- Hydrometallurgisches Recycling: Auflösen von Fraktionen und chemische Rückgewinnung (Fällung, elektrochemische Abscheidung) der Elemente
Herausforderungen
Häufig werden die einzelnen Verfahren miteinander kombiniert, um so bessere Ergebnisse zu erzielen. Jedoch ist der Einsatz von Energie und Prozessmitteln je nach Verfahren noch recht hoch. Neben bereits etablierten Verfahren zur Rückgewinnung von Kupfer, Aluminium, Nickel, Kobalt und Mangan besteht noch Bedarf an effizienteren Prozessen, um auch andere Bestandteile wie Graphit oder Lithium wieder zurückzugewinnen. Lithiumbatterien sind wegen der darin enthaltenen wertvollen Metalle (Kobalt und Nickel) bereits heute schon rentable Abfallströme. Jedoch sollte im Sinne der werkstofflichen Kreislaufwirtschaft nicht nur die Rückgewinnung der Metalle, sondern die Wiederverwertung der höherwertigen Funktionsmaterialien (der Batterieelektroden) ermöglicht werden. Dies trägt dazu bei, die Elektromobilität zu einer rundum nachhaltigen Alternative zu herkömmlichen Antriebstechnologien zu entwickeln (neben der Bereitstellung klimaneutraler Elektrizität). Dazu muss die gesamte Recyclingkette von Batterien effizienter werden. Speziell steht das Recycling von Elektroautobatterien in Deutschland noch vor folgenden Herausforderungen:
- Altfahrzeuge werden (teilweise auf nicht legalem Weg) in andere Länder exportiert, anstatt sie einem Recycling in Europa zielgerichtet zuzuführen.
- Noch immer herrscht eine hohe Unsicherheit über die Rückläuferentwicklung. Dies hat zur Folge, dass Recyclingkapazitäten aufgrund fehlender Planungssicherheit mittelfristig nicht ausreichen werden, da die Unternehmen die Investitionen scheuen.
- Die Rückführlogistik ist noch nicht ausreichend aufgebaut, um von der Sammlung, über den Transport bis hin zur Verwertung sichere und effiziente Prozesse abzubilden.
- Hochleistungsbatterien gehören zu den Gefahrgütern. Dies bezieht sich nicht nur auf giftige Inhaltsstoffe wie beispielsweise Fluorverbindungen, sondern auch auf das bestehende Brandrisiko. Dies ist für jeden Schritt des Recyclingprozesses zu beachten und stellt hohe Anforderungen an Lagerung, Transport, Handling sowie das Recycling selbst.
- Es gibt keine einheitlichen Batteriesysteme. Dies bedeutet, dass Batterien verschiedener Hersteller auch unterschiedlich aufgebaut sind. Das erschwert eine automatische Zerlegung und effizientes Recycling. Hinzu kommt, dass die Komponenten nur schwer voneinander zu trennen sind, z.B. durch Verklebung oder Verschweißen der Einzelzellen und der Gehäuse.
- Die bereits etablierten Prozesse wie die Pyrometallurgie bieten für bestimmte Stoffe eine hohe Rückgewinnungsrate bei hohem Energieeinsatz. Ein Teil der Rohstoffe (vor allem die unedlen Metalle und der Kohlenstoff, also z.B. Graphit) gehen verloren. Zusätzlich werden bei der Hydrometallurgie große Mengen an Prozessmitteln wie Chemikalien eingesetzt, die nach Abschluss des Prozesses wiederum einer fachgerechten Entsorgung zugeführt werden müssen.
Lösungsansätze
Es ist sicherlich noch ein weiter Weg, bis ein geschlossener Kreislauf in der Industrie etabliert ist. Nichtsdestotrotz gibt es bereits vielversprechende Ansätze, wie dies gelingen kann. Die Forscher der Fraunhofer-Projektgruppe IWKS empfehlen daher:
- immer den gesamten Wertstoffkreislauf der Batterien zu betrachten und nicht Verfahren unabhängig voneinander für einzelne Teilbereiche zu etablieren.
- alle betroffenen Akteure, insbesondere Designer, Hersteller, Nutzer, Recycler und Kunden des Recyclingprodukts, einzubinden.
- Logistikströme mit fest definierten Prozessen zu entwickeln – von der Sammlung, über den Transport bis hin zur Lagerung.
- neue Ansätze bei Sammlungs- und Transportkonzepten zu gehen. Dazu muss u.a. die Rücknahmestruktur in Kooperation mit den Herstellern verbessert und ökonomische Anreize geschaffen werden. Die Konzepte müssen so gestaltet werden, dass ein Recycling nicht zusätzlich erschwert wird. Hierzu zählt zum Beispiel die Sicherstellung eines möglichst sortenreinen Stoffstroms.
- Sicherheitsrisiken bei Lagerung und Transport direkt in Recyclingkonzepte einzubeziehen und so zu minimieren.
- die Weiterentwicklung alternativer, innovativer Zerkleinerungs- und Trenntechnologien wie die elektrohydraulische Zerkleinerung, bei denen das Aktivmaterial Nickel-Mangan-Kobalt und der Graphit als Pulver leichter von den anderen Bestandteilen zu trennen sind. Ziel dabei sind die Reduzierung von Energie- und Prozessmittelverbrauch und die nahezu vollständige Rückgewinnung aller Bestandteile der Batterie.
- Möglichkeiten zur Automatisierung im Recyclingprozess voranzutreiben, u.a. durch verbesserte Kennzeichnung der verschiedenen Batterietypen und Verpflichtung der Hersteller durch Normierungen.
- eine konsequente Umsetzung eines Design for Recycling, d.h. Entwicklung und Umsetzung einheitlicher Konzepte, die die Wiederverwertung von Batterien und Akkus direkt bei der Entwicklung berücksichtigen (Voraussetzung für automatisierte Recyclingverfahren). Hierfür müssen alle Akteure miteinbezogen werden, also Hersteller, Zulieferer, Automobilbauer und Recycler.
- frühzeitig die Übertragung erfolgreicher Kreislaufkonzepte auf ähnliche Produkte prüfen, wie beispielsweise stationäre Energiespeicher.
Im Rahmen des Projekts NeW-Bat wurde Material gebrauchter Batterien erfolgreich direkt für die Fertigung neuer Zellen eingesetzt. Damit könnte der stoffliche Kreislauf der kritischsten Bestandteile von Lithiumbatterien geschlossen werden – vorausgesetzt, die notwendige Infrastruktur und Rahmenbedingungen werden entsprechend aufgebaut.
Quellennachweise:
(1) Quelle: https://de.statista.com/statistik/daten/studie/406683/umfrage/anzahl-der-verkaeufe-von-elektroautos-weltweit-prognose/ und
https://www.bundesregierung.de/breg-de/themen/energiewende/elektromobilitaet-weiter-vorantreiben-1530062
(2) Richa, K. et al : A future perspective on lithium-ion battery waste flows from electric vehicles. In: Resources, Conservation and Recycling, Elsevier, Volume 83, February 2014, Pages 63-76, https://www.sciencedirect.com/science/article/pii/S092134491300253X?via%3Dihub
(3) Hu, Y., Cheng, H, Tao, S.: Retired Electric Vehicle (EV) Batteries: Integrated Waste Management and Research Needs. In: Environmental Science & Technology, 2017, 51 (19), pp 10927–10929, https://pubs.acs.org/doi/full/10.1021/acs.est.7b04207?src=recsys
(4) Quelle: Verordnung zur Durchführung des Batteriegesetzes, §3 Behandlung und Verwertung, http://www.gesetze-im-internet.de/battgdv/__3.html
(5) Quelle: RICHTLINIE 2006/66/EG DES EUROPÄISCHEN PARLAMENTS UND DES RATES vom 6. September 2006, https://eur-lex.europa.eu/legal-content /DE/TXT/HTML/?uri=CELEX:32006L0066&from=DE
(6) Quelle: Deutsche Rohstoffagentur, Stand: Juni 2018, https://www.deutsche-rohstoffagentur.de/DERA/DE/Downloads/DERA%202018_cdm_06_Rohstoffrisikobewertung_Kobalt.html