Closing the value chain in electromobility
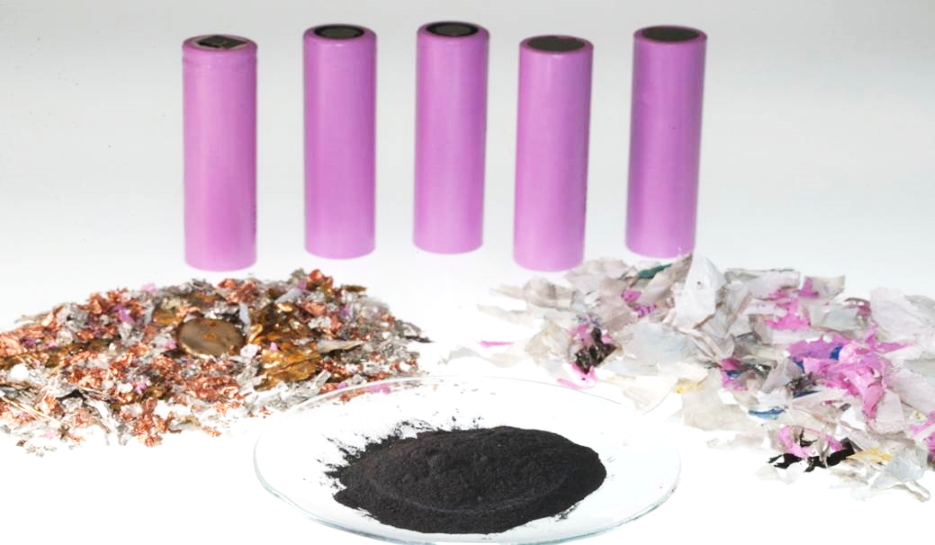
Strategic importance
Rechargeable batteries are used in a wide variety of applications and are becoming increasingly important. In addition to usage for mobile devices, power tools and stationary energy storage devices, applications in electromobility are particularly noteworthy. Large-format traction batteries made of high-performance Lithium-ion cells are the heart of modern electric vehicles and thus a key technology for the European automotive industry.
According to the current forecast of the National Platform Future of Mobility (formerly National Platform Electromobility), approximately one million electric cars are expected to be registered in Germany alone by 2022. The experts estimate that the number of electric vehicles in Germany will rise to 2 to 3 million by 2025. For automotive applications, the service life of batteries is limited and ranges from a few years to 10 years or longer, depending on battery type and load. This means that a steadily growing number of used traction batteries can be expected in the near future.
These batteries contain valuable and sometimes also supply-critical resources such as cobalt, lithium, nickel and copper, which mostly have to be imported from countries outside the EU. They also contain substances that would endanger our environment and health if they were disposed of improperly. Effective battery recycling is therefore of great relevance from both an economic and an ecological point of view.
In order to make e-mobility more sustainable, to secure important resources for the key technology of Lithium-ion batteries and to prevent unnecessary environmental pollution, innovative recycling processes for industrial large-scale applications must be further developed in the near future and closed material cycles for battery materials must be established.
Challenges
Various commercial recycling processes are already being successfully used today for the recycling of traction batteries. These usually comprise a combination of mechanical and hydro- and/or pyrometallurgical process steps and thus enable the material and energy recovery of battery materials. However, in terms of sustainability, environmental compatibility, efficiency and scalability, potential improvements can be identified for battery recycling. From the point of view of the Fraunhofer IWKS, the following challenges are particularly relevant:
- Design of processes and logistics for the expected return flow quantities from the e-mobility sector, in particular during dismantling
- Reduction of energy consumption and CO2 emissions as well as savings of process resources and costs in battery recycling
- Increasing recycling efficiency according to the EU definition, i.e. increasing the proportion of recycled battery materials
- Return of recycled material to the production of new battery cells or the creation of closed material cycles
- Safe handling of battery systems, especially in the event of damage - for example batteries from accident vehicles
- Flexibility with regard to different system designs, cell types and material compositions - also taking into account new technologies such as solid state batteries
- Establishment of re-use concepts for used battery systems, modules, cells and components, taking into account product warranty requirements
Solution approaches
In order to meet these challenges and to establish forward-looking recycling processes in good time, increased and joint development work is necessary. To this end, partners along the entire value chain must be involved, i.e. material manufacturers, cell and system manufacturers, plant constructors, car manufacturers as well as logistics and recycling companies. The Fraunhofer IWKS researchers are working on new concepts and innovative technologies within the framework of various national and European cooperations. The most important approaches of the institute and its partners are described below:
- Generation of return flows from old products that are as pure as possible and thus can be recycled more efficiently through suitable take-back and logistics concepts
- Establishment of safe, non-destructive and cost-effective methods for the detection of charge and aging states of battery cells
- Digitization and automation of battery disassembly as far as possible as well as development of alternative disassembly solutions through innovative fragmentation technologies
- Material selective fragmentation of battery cells in liquid medium for passivation of pollutants and efficient separation of material composites
- Enrichment of recyclable materials - especially active materials - through innovative separation and sorting processes in the first stage of recycling (Fig. 1)
- Recovery and processing of functional materials (already synthesized compounds) instead of metallurgical separation into individual elements
- Design for Recycling" and "Design for Disassembly" of the batteries by unification of the design forms, easily separable connections as well as labels and markers